Strautmann’s innovative 52M3 Magnon Forage Wagon is proving a formidable ally for a Carmarthenshire contractor
Keen to maximise the efficiency of his 600ha-a-year silage operation, Gary Morgan invested in a state-of-the-art Strautmann Magnon 10-530 forage wagon.
Thanks to its large body and pivoting headboard, this top-of-the-range model has sufficient capacity to carry 52m3 of grass per load, helping him cover his beat in and around the village of Blaenwaun in a timely fashion.
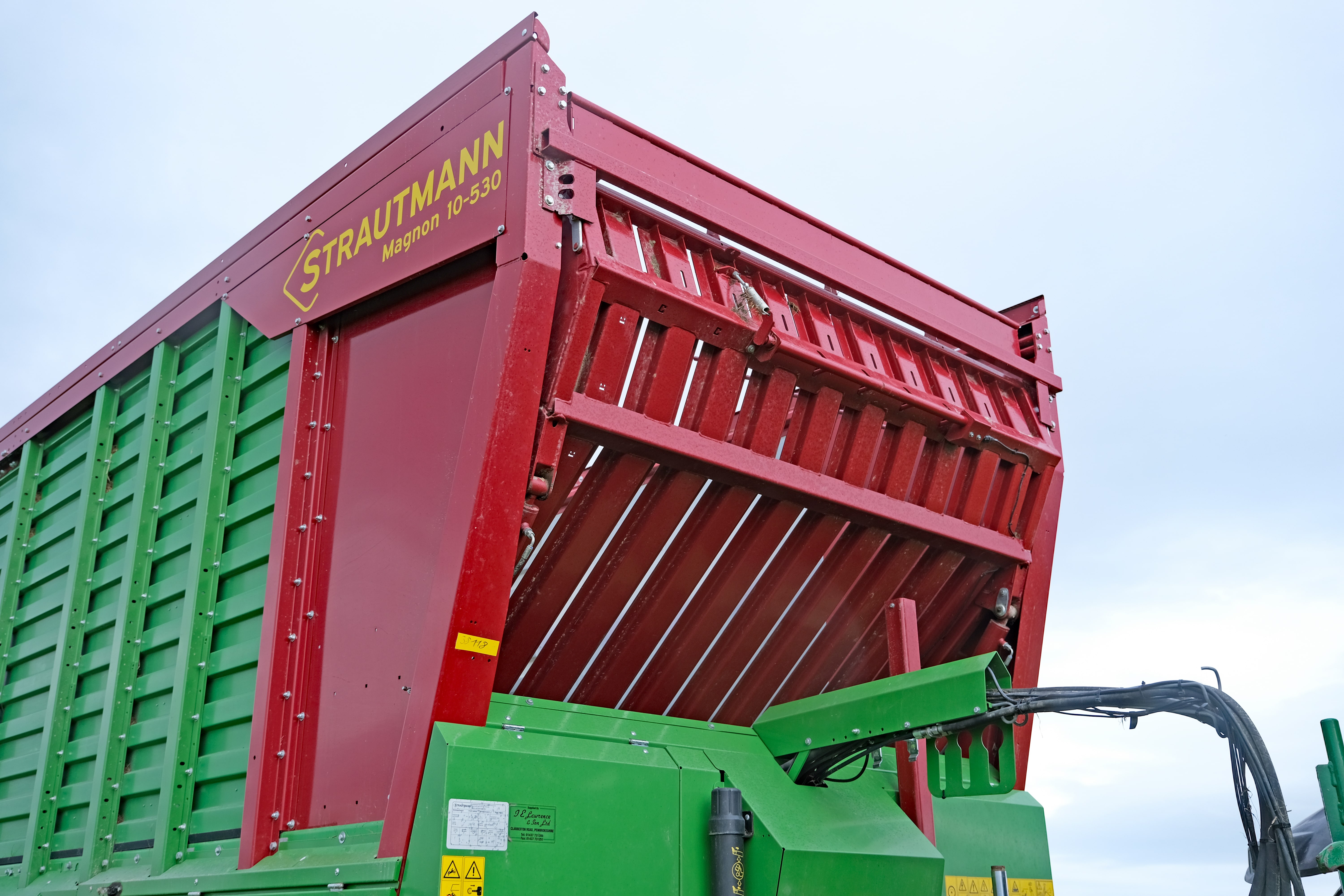
Added to that, innovative features such as plastic-tines on the Flex-Load pickup, Continuous Flow System roller and Exact-Cut chopping unit have boosted efficiency and reduced downtime.
Together, these make average outputs of 20ha a day possible, with 30ha or more achievable in lighter crops, or where he only has to travel short distances to the clamp.
Gary isn’t new to the Strautmann brand, having run one of the German maker’s Giga 4 models for 14 years. He couldn’t fault the build quality of this machine, but felt the time was right to upgrade, particularly given how much technology had progressed on the latest wagons.
“I’d been wanting to upgrade for a while, but I knew the Magnon was coming and liked the look of the new features so I held off until early this year so that I could get one,” he says.
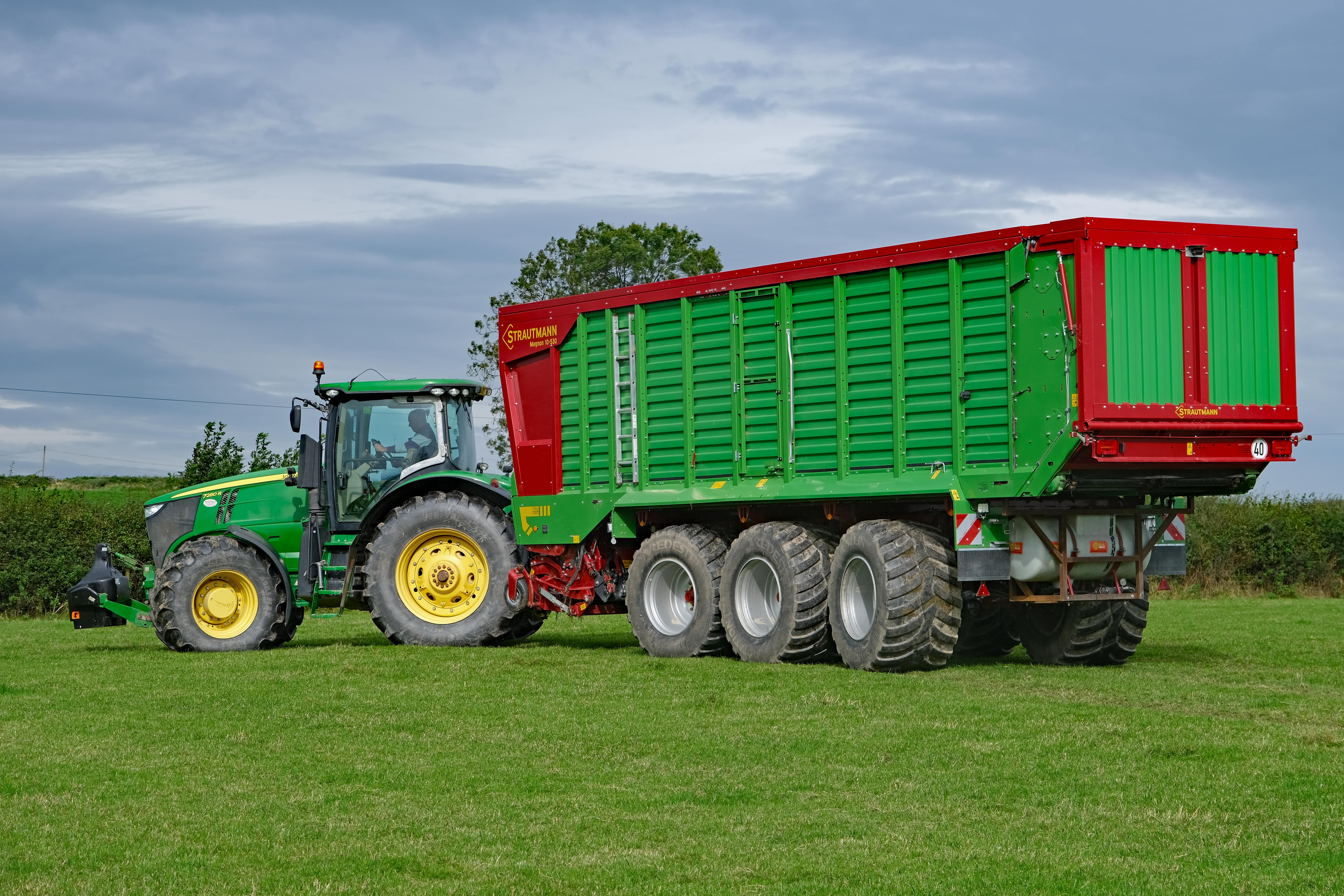
Extra capacity
One piece of technology that interested him in particular was the hydraulic headboard, which increases capacity by making use of the vacant space above the pickup and chopping unit.
When the main body is full, this automatically pivots forward creating extra space for squeezing in more grass. As most of his jobs require a mile or so of driving from field to clamp, this reduces the number of journeys he has to make.
The Continuous Flow System also makes the most of the machine’s capacity. This is thanks largely to the powered roller positioned between the pickup and chopping unit.
Featuring a spiral bar around its circumference like a shallow auger, this pulls material as it comes off the pickup both backwards and slightly outwards, ensuring that an even mat of crop is presented across the entire width of the knife bank. It also reduces the load on the pickup as the feed rotor starts to compress the crop as it comes off the roller and not the pickup tines.
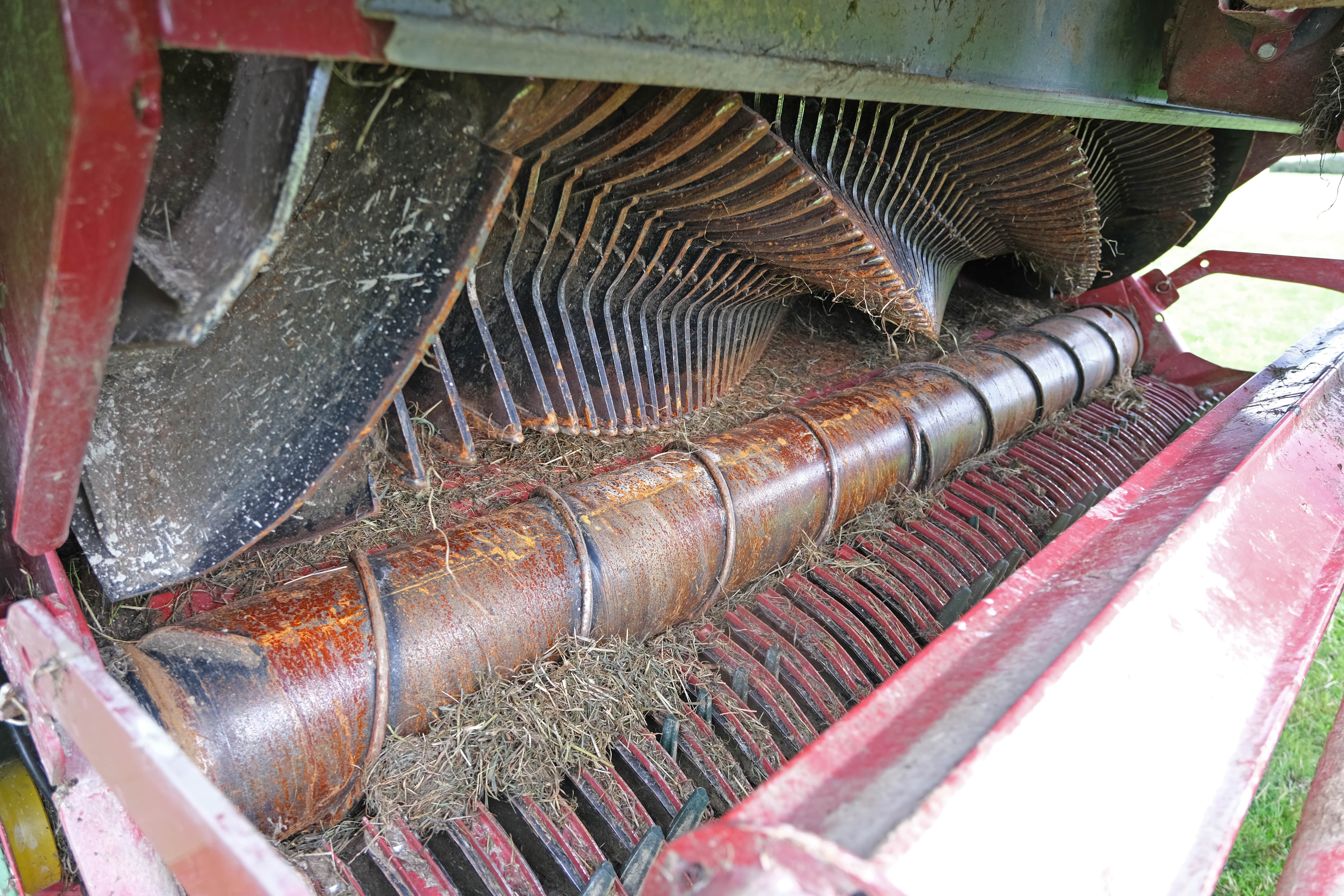
“You wouldn’t think the bars would make that much difference, but I can clearly see the grass being levelled out by it,” says Gary.
One noticeable benefit is that the body of the wagon is loaded more evenly, with a flat rather than domed profile to the grass. “I’ve got a camera in the back and it’s amazing to watch how squarely it fills without any unused space at the sides,” he says.
Consistent chop length
It also results in a more consistent chop length as every knife in the bank is tasked with processing roughly the same quality of crop.
With 48 of these in place, theoretical length of cut is 35mm and Gary says customers are seeing very little variation across loads. This helps produce higher-quality and more consistent silage.

An added bonus is that blades wear more evenly. “On the old machine the central knives used to take all the strain, so I regularly had to swap them with the outside ones – I haven’t had to move any yet on this machine.”
Having plenty of open space under the knives also means that chaff doesn’t get wedged between, removing the need to periodically clean them out.
Plastic pickup tines
Often having to work on rough, undulating ground, Gary has been won over by the Flex-Load pickup and its tough-yet-flexible plastic tines.

Unlike metal versions that can bend, snap and cause damage to the metal pickup bands, these deflect when they hit obstacles, before quickly returning to their original shape.
After a full season of work, he hasn’t had to change a single tine or band and they are showing virtually no signs of wear.
“It’s been a huge time saving and I’ve really appreciated not having to crawl around and bang my head replacing them.”
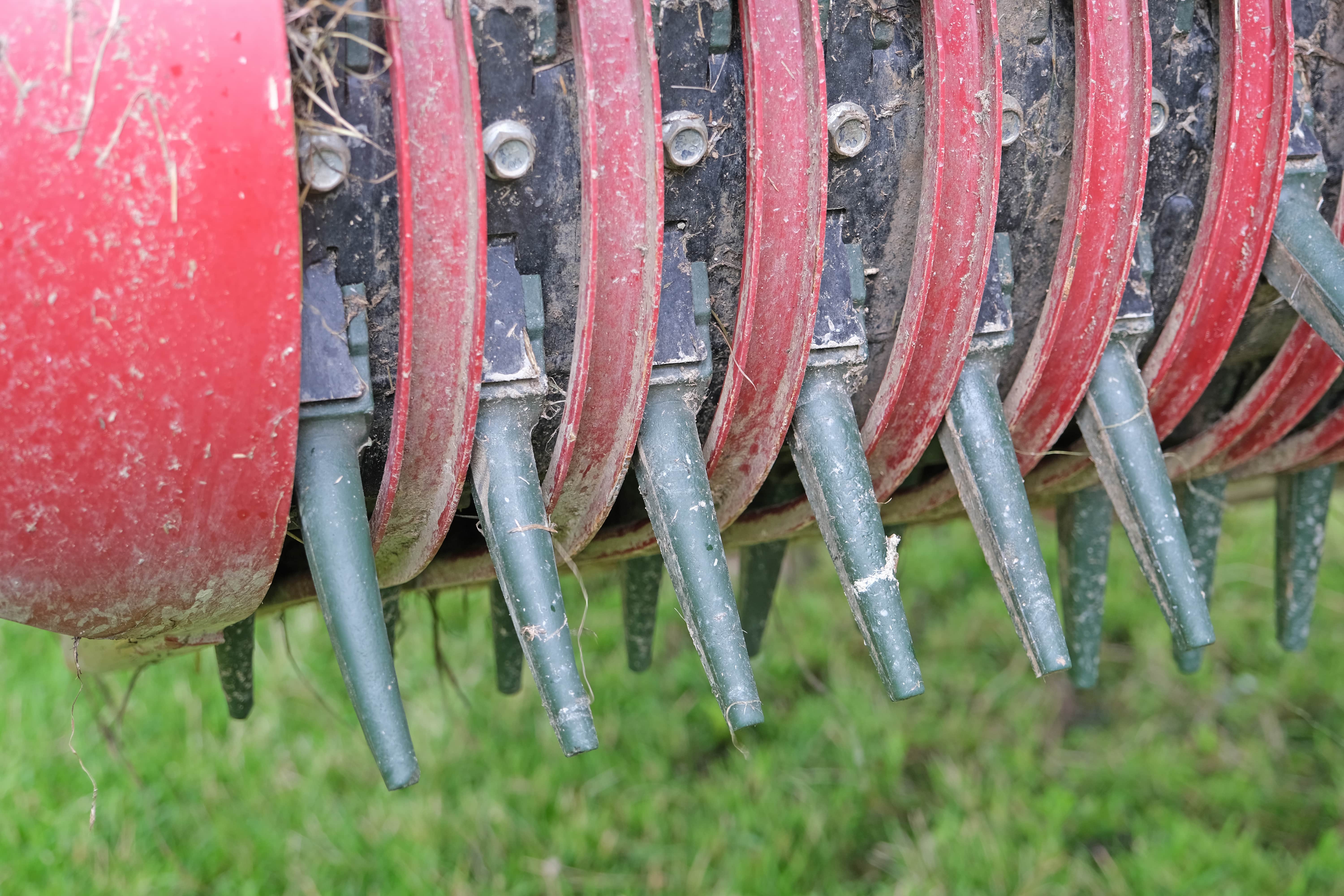
Another component that helps protect the pickup on uneven terrain is the optional support roller, which is centrally mounted at the rear of the pickup unit.
This sits slightly higher than the regular side-mounted wheels, allowing the assembly to move as normal on flat ground. However, when the pickup wheels drop into a dip, it prevents the tines bashing into the ground.
Thanks to the pick-up’s generous 2.25m width, there’s also no risk of crop spilling out, even in bulky swaths rowed up by four-rotor rakes.
Tri-axle chassis
As Carmarthenshire is rarely short of rainfall, Gary took the decision to spec his wagon with triple axles running on huge 800/45 R30.5 floatation tyres.
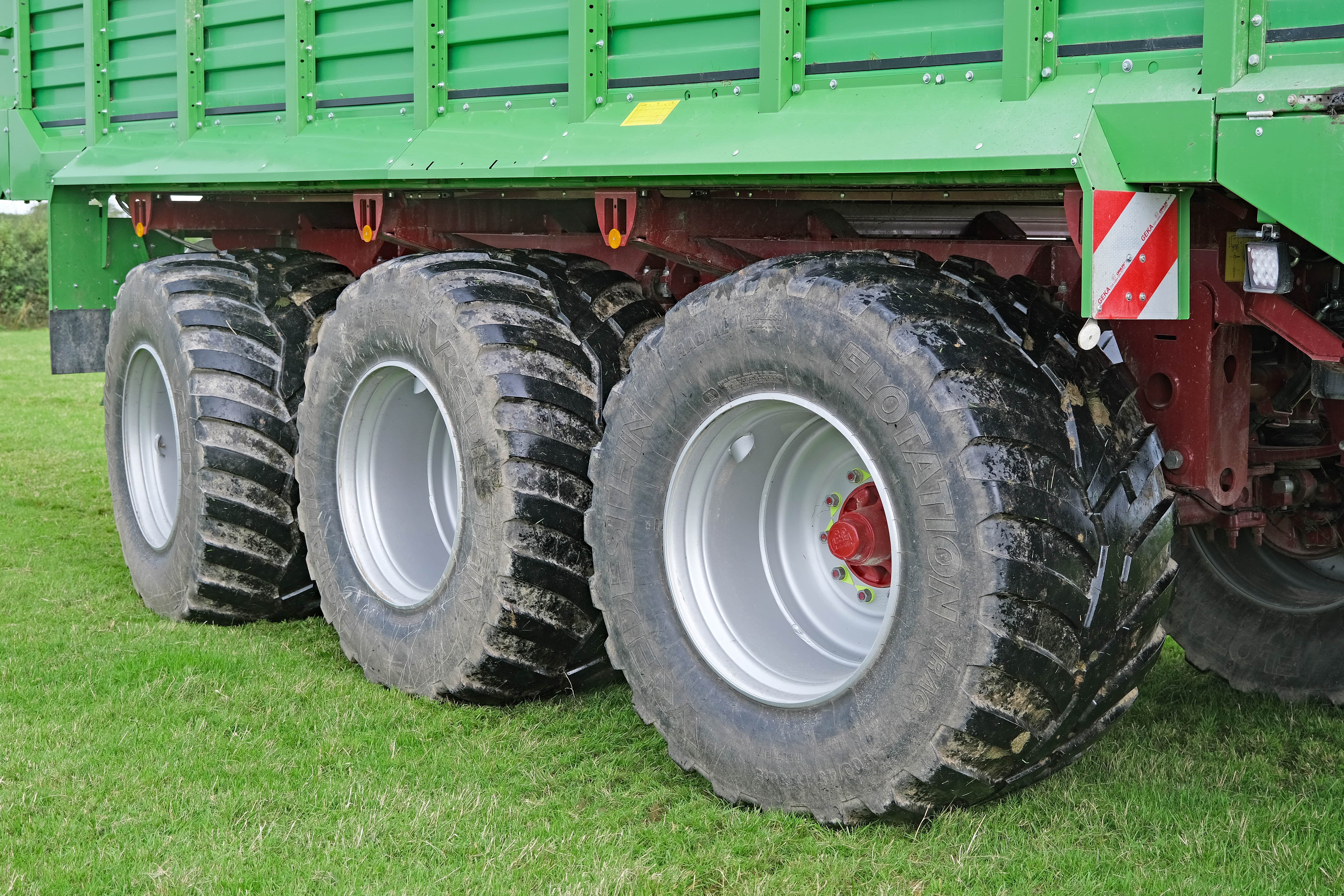
These do a stellar job of spreading the load, so much so that customers have commented on the fact that they can’t see where he’s been.
In addition, the Active Steering Axel system for the front and rear axles allows him to thread the wagon through some incredibly tight spaces. Given the amount of narrow lanes and tight yards in his area, this has proved invaluable.
The Active Steering system also comes into its own on steep sidehill ground. While passive systems need to be locked in work and unlocked on the headlands, creating some undesirable handling on the steeps, the active system is far more predictable.
“It’s so much more planted and wherever the tractor goes it follows,” says Gary.
To make sure he doesn’t have any scrapes, he’s gone to the trouble of fitting cameras on either side of the machine and at the rear, all of which feed into two screens mounted in the cab.
Another welcome feature of the tri-axle setup is the load-sensing hydraulic suspension. This, combined with the secure K80 ball hitch, gives the outfit a particularly smooth ride and reduces operator fatigue.
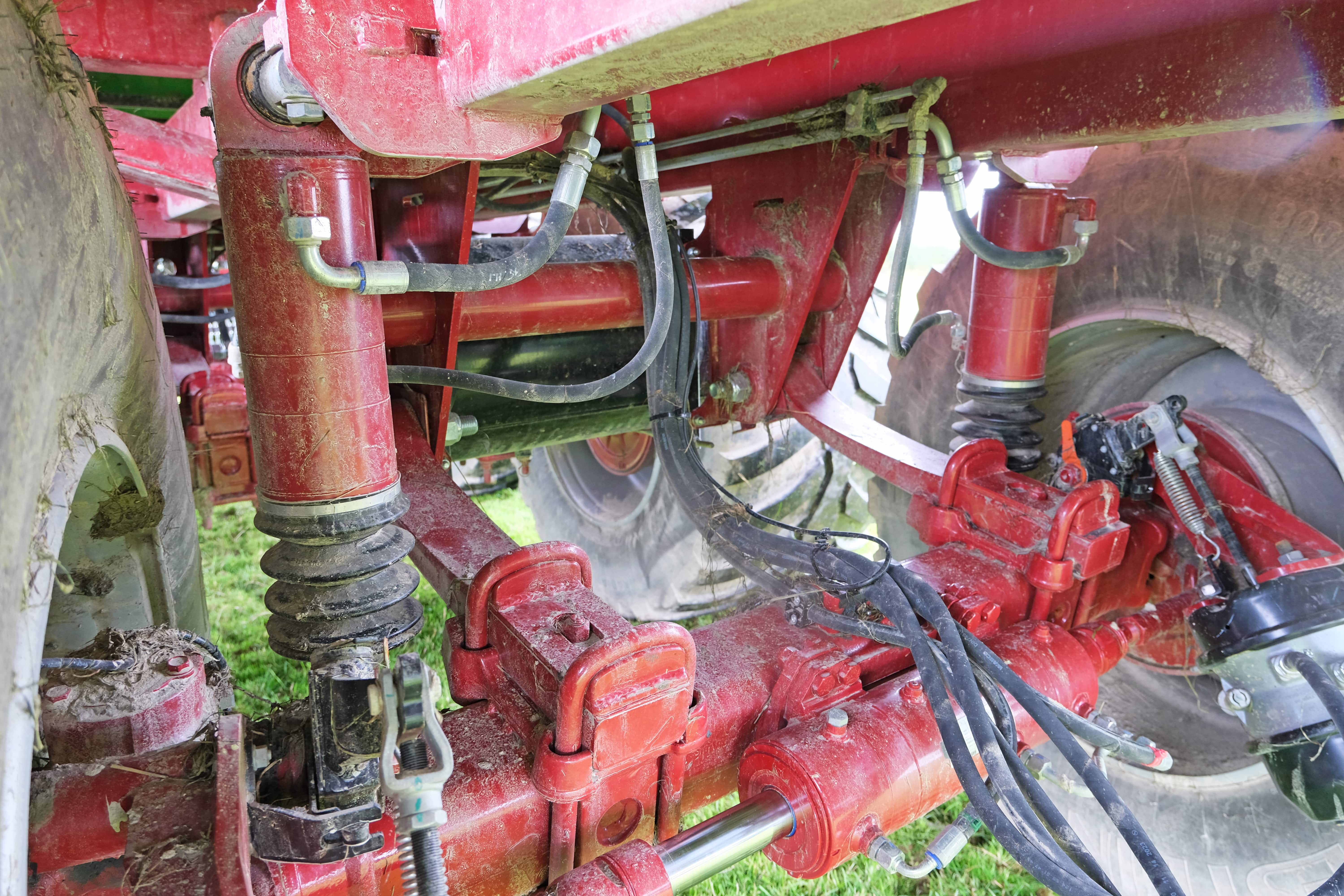
Setup is simple, with the suspension accumulators charged to the correct pressure via a single spool valve in the tractor, before being closed off to run as a sealed system.
The rest of the machine’s hydraulic functions run off the load-sensing hydraulics on Gary’s John Deere 7280R.
This includes drive to the pickup, bed chains and tailgate, as well as rams for lifting wheels on the front axle, leaving just the chopping cylinder and flow roller to be run by the tractor’s pto.
Simple to use
All of the machine’s functions are controlled via ISOBUS but, for ease of use, Gary opted for a dedicated Strautmann SMART 570 5.5” touch screen controller rather than using the display in his tractor. This shows all machine functions clearly, making it blissfully simple to operate.
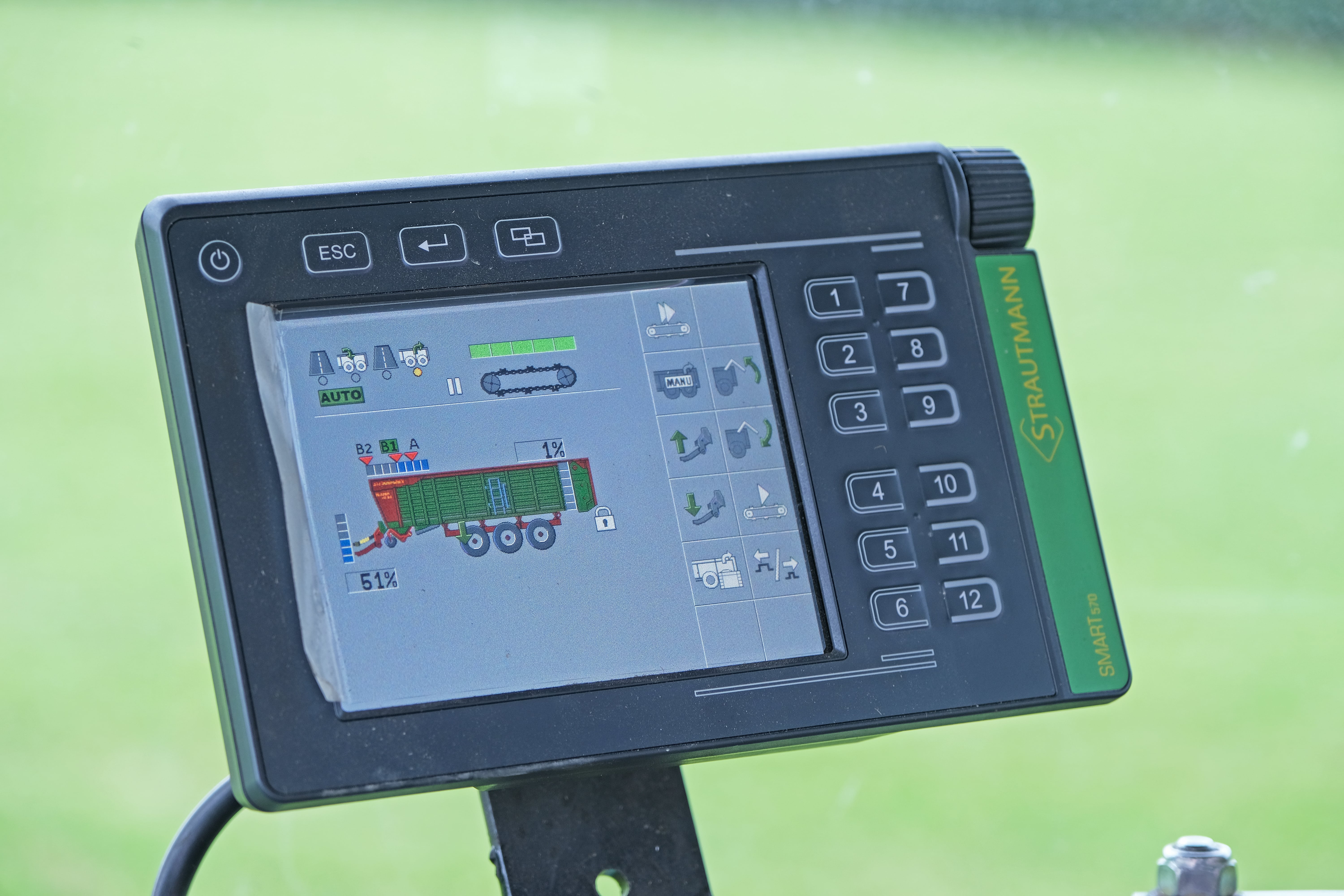
For added convenience, most of the wagon’s functions are automated, meaning Gary only has to press one button to put the machine into work and one to lift it out at the headland.
This means the bed chains and headboard will all move automatically to fill the wagon in the most efficient way.
It’s a similar story with unloading, where there’s a timed sequence for opening the tailgate and running the bed chains and moving the headboard to jettison the load.
Simple to maintain
Strautmann has also gone to considerable lengths to reduce the maintenance burden on the Magnon.
This has meant grouping all regular grease nipples in banks on the side of the machine making it easier to grease.
“There was a fair bit of grovelling involved when going around the old machine with the grease gun, but it’s a piece of cake on this one,” says Gary.
His only modification has been to fabricate a frame that bolts under the rear of the body to support a 400-litre additive tank. This is piped to two nozzles positioned above the pickup.
His dealer, JE Lawrence, wired the pump so that it switches on and off automatically as the machine is put in and out of work.
Gary Morgan’s Strautmann Magnon 10-530
Capacity: 52m3
Pickup: 2.25m Flex-Load with plastic tines
Cutting unit: Exact-Cut rotor with 48 knives
Theoretical chop length: 35mm
Length: 11.78m
Outside wheel width: 2.81m
Chassis: Triple axles with hydraulic suspension and mechanical forced steering
Tyres: Vredestein 710/50 R26.5
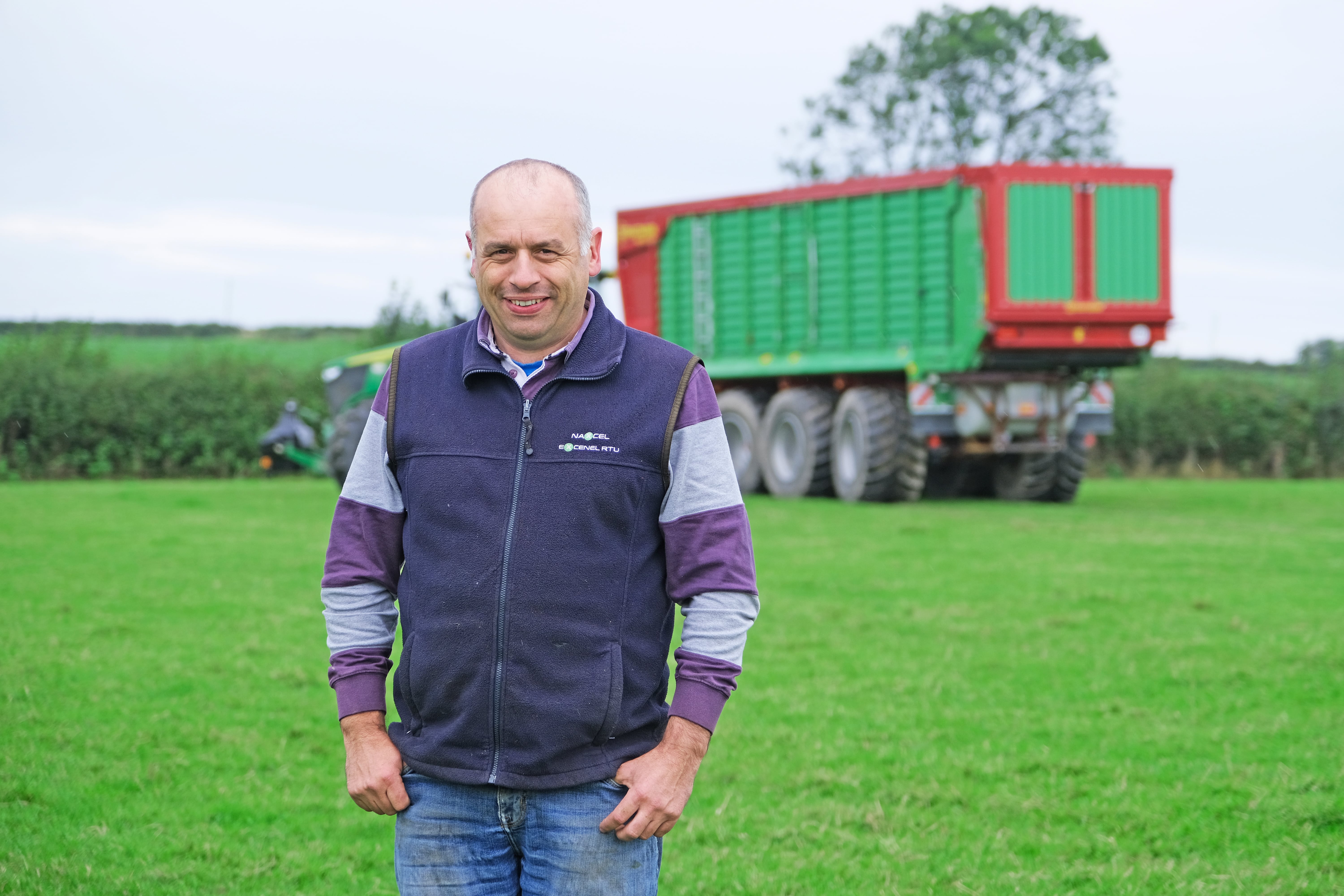
Opico Company News

